مقدمه
با توجه به افزایش رشد نیاز جهان به فولاد به عنوان مهمترین ماده اولیه ساخت و ساز، تولید فولاد در جهان نیز رشد تصاعدی داشته است؛ به طوری که در طی 12 سال گذشته، 45 درصد افزایش داشته و حدود 8 درصد از مصرف انرژی در کل جهان، برای تولید فولاد خواهد بود. همین موارد موجب شده تا کاهش مصرف انرژی در صنایع فولادی، بسیار ضروری باشد.
مسئله کاهش مصرف انرژی به دلایل مختلفی نظیر ارزانی حاملهای انرژی در صنایع فولادی در ایران، چندان مورد توجه قرار نگرفته است. با توجه به سهم حداقل 20 درصدی انرژی در قیمت تمام شده فولاد و واقعی شدن قیمت حاملهای انرژی در سالهای اخیر، موضوع کاهش مصرف انرژی در صنایع فولادی را به یک موضوع حیاتی تبدیل کرده است.
در این مقاله، تلاش شده تا عوامل تأثیرگذار بر مصرف انرژی در کورههای قوس و القایی مورد بررسی قرار گیرد و راهکارهای کاهش مصرف انرژی در صنایع فولادی بیان شود. برای کسب اطلاعات بیشتر در این زمینه، با ما تا انتهای مقاله همراه باشید.
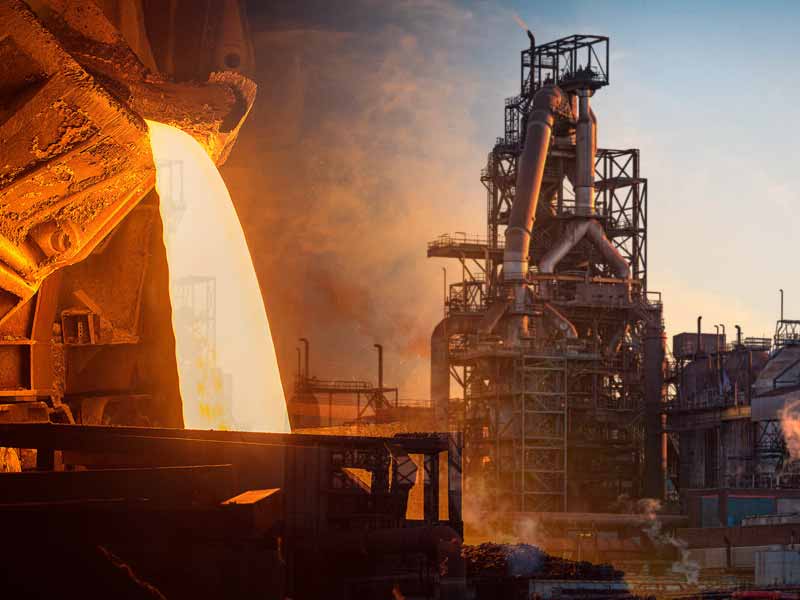
راهکارهای کاهش مصرف انرژی در چرخه تولید فولاد
به طور کلی، برای بهبود راندمان و کاهش مصرف انرژی در چرخه تولید محصولات فولادی، راهکارهای بسیاری وجود دارد که این امر، موجب بهبود کارایی در روش کوره بلند نیز خواهد شد. بدین منظور، توصیه میشود تولید فولاد با استفاده از تکنولوژیهای تزریق در کوره بلند، سنسورها، کنترل فرآیند و ماکزیمم شدن قراضهها و اکسیدها انجام شود.
علاوه بر این امر، با نصب سیستمهای مدیریت و مانتیورینگ انرژی برای بازیابی و توزیع بین فرآیندها، کنترل کردن میزان رطوبت زغال، تزریق گازهای BOF و COG و سایر موارد زیر به کاهش مصرف انرژی و بهبود راندمان کوره بلند القایی کمک کرد:
- بازیابی گاز کوره بلند
- بهبود سیستم کنترل داخل کوره بلند
- بازیابی حرارت حاصل از سرباره
- توربینهای بازیابی فشار بالا
- اتوماسیون، رکوپراتور و بهبود احتراق در گرمخانه هوای دم
- شارژ آگلومرههای کامپوزیت کربن
برای کاهش مصرف انرژی در کورههای اکسیژنی و قوس باید سه نکته مهم رعایت شود؛ این نکات شامل بهتر شدن میزان کنترل و مانیتورینگ فرآیند احیا، گرم کردن پاتیل مفید و برنامهریزی شده و بازیابی گاز سوخت و حرارت BOF خواهد شد.
مورد بعدی در بهینهسازی انرژی در عملیات ریختهگری است که بعد از تولید قطعات نیمهنهایی تأثیر بسزایی در خرید ورق سیاه و قیمت فولاد دارد. تولیدکنندگان صنعت فولاد میتوانند با گرمادهی تاندیش و پیشگرم کردن پاتیل از قبل و همچنین انجام فرآیند ریختهگری به شکل نهایی محصول، موجب کاهش مصرف انرژی و در نتیجه کاهش هزینههای تولید شوند.
بهبود مصرف انرژی در واحد نورد گرم
به منظور بهبود مصرف انرژی در واحدها و فرآیندهایی که برای انجام نورد گرم مورد استفاده قرار میگیرد، نکات مهمی باید رعایت شود. همانطور که مشخص است، کیفیت ورقهای سیاه، میلگرد، تیرآهن، محصولات اسیدشویی و سپس ادامه تولید قطعات تخت فولادی با توجه به این واحد مشخص خواهد شد.
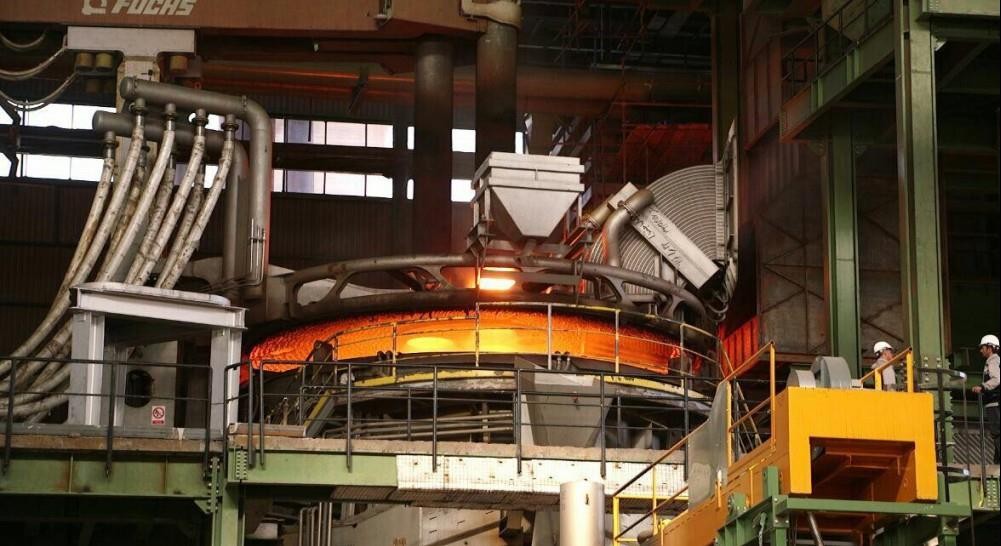
بنابراین، بهتر است به این مورد نیز توجه داشته باشید که کیفیت موارد گفته شده، در قیمت و خرید محصولات نهایی، یعنی ورقهای گرم و سایر فلزات تولیدی از این ورقها نیز تأثیرگذار خواهد بود. این فلزات، هر کدام بسته به خواصی که دارند، کاربردهای بسیاری در صنایع داشته و جزو مواد اولیه اصلی به شمار میروند.
به طور مثال، انواع ورقهای سیاه دارای سطح زبر و رنگی کدر هستند و به دلیل وجود گریدهای متنوع از این محصول، در فرآیندهای زیادی، مورد استفاده قرار میگیرند. اما در صورتی که نیاز به ورقهایی با ظاهر بهتر، صافتر، صیقلیتر و روشنتری باشد، باید از انواع ورقهای سرد و گالوانیزه استفاده کرد که دارای مقاومت بالاتری در برابر خوردگی و زنگزدگی هستند. با این وجود باید در نظر داشت که در صورت نیاز به ورق گالوانیزه، باید به فکر کاهش هزینههای مصرف انرژی در کارخانجات تولید مواد اولیه این فلزات نیز بود. از همین رو، راهکارهای بهبود و کاهش مصرف انرژی در صنایع فولادی در بخش نورد گرم، در ادامه بیان شدهاند:
- بهتر است دمای پیشگرم به حدود 1200 درجه سانتیگراد برسد.
- شارژ حرارت و بازیابی حرارتی
- استفاده از مشعلهای رکوپریتیو
- تنظیم تمامی عملیاتها در نورد گرم
- استفاده از مشعل در کوره آنیل با شعله نامرئی
- عایقکاری کورهها موجب کاهش مصرف انرژی خواهد شد.
- بازیابی حرارت هدر رفته از بسترهای آب خنککننده
روشهای کاهش مصرف انرژی در عملیات نهایی و نورد سرد
واحد نورد سرد و عملیات نهایی در جهت تولید ورقهای روغنی و سرد مورد استفاده قرار میگیرند که ماده اولیه اصلی آنها نیز همان ورق سیاه است. البته ورق سیاه مورد استفاده در این واحدها، ابتدا در طی عملیاتهای مختلفی دچار بهبود در خواص مکانیکی، عملکرد نهایی، کاهش صخامت و زیباسازی میشوند.
خرید ورق سرد یا ورق روغنی نیز با توجه به هزینههای اولیه و میزان انرژی مصرف شده برای تولید آن، تعیین میگردد؛ اما معمولاً به علت خواص بهتر و بیشتر این نوع ورقها، قیمت آنها در مقایسه با ورق سیاه یا ورق گرم، بیشتر است.
راهکارهای کاربردی و مناسب در جهت کاهش مصرف انرژی در واحدهای عملیات نهایی و نورد سرد در ادامه بررسی شدهاند:
- بازیابی حرارت در کورههای بازپخت یا آنیل
- استفاده از کوره آنیل پیوسته
- هدفگذاری اتوماتیک و مشخص کردن خواص نهایی محصول
- کنترل و تنظیم سیستمهای پایش
- کاهش مصرف بخار در خط اسیدشویی که در جهت پاکسازی شیتها انجام میگیرد.
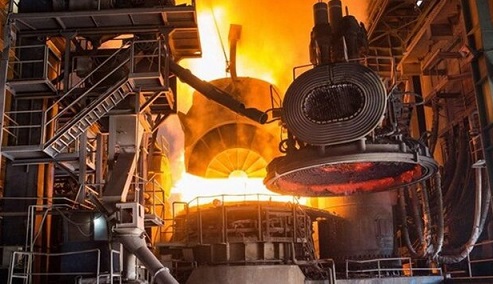
مصرف انرژی مربوط به فرایند فولاد سازی EAF
راهکارهای کاهش مصرف انرژی در کورههای احیایی یا کوره میدرکس در ادامه بررسی میشوند. اما قبل از بررسی این راهکارها باید به نکته توجه داشت که ورقهای فولادی و قطعات نیمهنهایی در ایران به وسیله روش میدرکس و بر پایه کورههای قوس الکتریکی تولید خواهند شد.
در واقع در این کورهها، علاوه بر افزایش سرعت تولید، انرژی کمتری نیز مصرف شده و از همین رو، هزینههای تولیدی مواد اولیهای نظیر اسلب فولادی، بیلت، بلوم و غیره کاهش یافته و قیمت قطعات تخت فولادی از جمله ورق سیاه، ورق ST52، اسیدشویی، گالوانیزه، روغنی و غیره نیز به مراتب کمتر میشود.
راهکارهای مورد نظر به شرح زیر هستند:
- افزایش سرعت منتقل شدن انرژی الکتریکی در کورههای قوس
- افزایش سرعت پیشگرم قراضه و عملیات شارژ
- کنترل کردن و مانتیورینگ زمان عملیات احتراق
- کاهش مصرف انرژی در عملیات زینترینگ و بازیابی حرارت در آن
- منتشر کردن بهینه زینترینگ
- کم کردن میزان نشتی هوا
- بیشتر شدن عمق بسترها
- استفاده از سوختهای هدر رفته و مازاد در واحد زینتر
- بهبود روش شارژ
- بهبود فرآیند کوره احتراق
- افزایش درصد power on time

جمعبندی
این مقاله به بررسی کاهش مصرف انرژی در صنایع فولادی پرداخته است. انواع راهکارهای کاربردی و مفید گفته شده، موجب بهبود فرآیندهای عملیاتی شده و هزینههای مصرف انرژی را کاهش میدهند.
تولیدکنندگان با رعایت نکات ذکر شده در فرآیندهای اصلی فولادسازی، به راحتی میتوانند مصرف انرژی را بهبود بخشیده و از هدر رفت انرژی جلوگیری کنند. از همین رو، واحدهای فولادسازی باید با استفاده از این راهکارها، راندمان تولید خود را بهبود بخشند و افزایش دهند و در نتیجه هزینههای تولید را کاهش داده و اقتصادیتر عمل نمایند.